熱處理對(duì)于壓鑄模具使用壽命的影響較大,據(jù)有關(guān)資料介紹,由于熱處理不當(dāng),造成壓鑄模具早期失效占整個(gè)壓鑄模具事故的 44%左右。鋼淬火時(shí)所產(chǎn)生的應(yīng)力,實(shí)際上是冷卻過程中的熱應(yīng)力與相變時(shí)的組織應(yīng)力疊加的結(jié)果,鋼淬火后處于高應(yīng)力低韌性狀態(tài),具有高硬度和強(qiáng)度,較脆,實(shí)際上不能使用。而淬火應(yīng)力是造成變形開裂的原因,并導(dǎo)致疲勞強(qiáng)度沖擊韌性降低。為此,鋼淬火后必須進(jìn)行回火,去除應(yīng)力。穩(wěn)定組織,提高韌性。
模具淬火前去應(yīng)力退火處理:由于模具機(jī)加工時(shí)產(chǎn)生較大的內(nèi)應(yīng)力,為防止與熱處理時(shí)產(chǎn)生內(nèi)應(yīng)力迭加,引起模具變形和開裂,故要求模具在機(jī)加工后、淬火前進(jìn)行一次去應(yīng)力退火處理。退火溫度 600~650℃,保溫時(shí)間按照厚度每 25mm 保溫 1 小時(shí)計(jì)算,保溫隨爐冷卻至 300℃(也有冷至 500℃)出爐空冷。
制定合理的熱處理工藝:淬火工藝采用多段預(yù)熱和嚴(yán)格控制升溫速度:1.2343/44 類型鋼屬于中碳高合金鋼,相對(duì)于低合金鋼其導(dǎo)熱性能較差。因此淬火加熱應(yīng)采用多段預(yù)熱(2~3 段),為 300℃、650℃、850℃預(yù)熱,目的是使工件心部和表面的溫度趨于平衡,以減少溫差產(chǎn)生的熱應(yīng)力。同時(shí)其升溫速度應(yīng)執(zhí)行緩慢加熱的原則(100~200℃/h),以減少加熱過程中產(chǎn)生的熱應(yīng)力。在高溫加熱階段可采用較快升溫速度(10~15℃/h)以縮短高溫加熱時(shí)間,防止晶粒粗大;防止工件過熱現(xiàn)象:若加熱階段溫度超過正常的淬火溫度(包括儀表失靈或工件擺放靠近加熱元件等引起的),隨著淬火溫度的提高,保溫時(shí)間的延長(zhǎng),晶粒普遍粗化,組織脆性增加,殘余奧氏體增加,球狀碳化物轉(zhuǎn)變?yōu)槎嘟菭钐蓟铮⑶矣芯W(wǎng)狀組織出現(xiàn),模具在使用過程時(shí)容易出現(xiàn)開裂;
淬火加熱介質(zhì)和冷卻介質(zhì)的選擇:當(dāng)今世界對(duì)于大型復(fù)雜精密模具多采用真空或保護(hù)氣氛下熱處理,以防止模具表面氧化脫碳,尤以真空高壓氣冷淬火工藝應(yīng)用普遍。但要注意,氣冷速度不能太低,那就要求氮?dú)獾膲毫Υ笮∽銐?,通常要求工件從淬火溫度?020~1050℃)冷至 538℃過程中,其表面冷卻速度大于等于 28℃/分,也有要求工件心部冷卻速度大于等于 28℃/分。如果該溫度段,冷卻速度太慢,則淬火后其顯微組織會(huì)有碳化物或其他轉(zhuǎn)變產(chǎn)物沿晶界析出,從而降低鋼的韌性,增加脆性,在使用過程中過早開裂。另外有條件者,對(duì)于特別復(fù)雜的大型壓鑄模具可采用分級(jí)等溫淬火,能有效的減少模具變形和避免開裂。
回火工藝:淬火后要及時(shí)回火。工件淬火后冷卻至 90~70℃應(yīng)立即進(jìn)行回火,因?yàn)楣ぜ慊鸷筇幱诟邞?yīng)力、低塑性狀態(tài),容易引起開裂;回火要充足。大型復(fù)雜壓鑄模具淬火后,通常進(jìn)行三次回火,每次回火時(shí)間按工件有效厚度每 25mm 保溫 1 小時(shí)計(jì)算,但不少于 4 小時(shí)。目的是減少組織轉(zhuǎn)變應(yīng)力和穩(wěn)定尺寸。
壓鑄模具壓鑄生產(chǎn)和維護(hù)注意事項(xiàng):模具的良好預(yù)熱:模具裝配后試?;蛘Ia(chǎn),必須預(yù)熱模具而且模溫要均勻。鋁鎂合金的壓鑄模具的預(yù)熱溫度建議在 250~320℃,建議采用模溫機(jī)預(yù)熱;模具預(yù)熱到 300℃,其沖擊韌性提高很快,但當(dāng)模溫低于 200℃時(shí),材料的沖擊韌性降低很多,脆性增加;經(jīng)過良好預(yù)熱的模具,其熱傳導(dǎo)率要比沒有良好預(yù)熱的模具高近 20%;模具澆注溫度與模具表面溫度(預(yù)熱溫度)之差越大,則熱應(yīng)力越大,越容易引起熱疲勞和龜裂。日本壓鑄協(xié)會(huì)編輯資料介紹,模具溫度從 250℃提高到 350℃,即澆注溫度與模具表面溫度之差減少 100℃,則模具壽命幾乎可以提高 10 倍。
制定正確的澆注工藝:澆注溫度要合理,不能太高。否則澆注溫度太高,雖然流動(dòng)性更好,但鑄件冷凝時(shí)間長(zhǎng),易產(chǎn)生縮孔,氣孔,容易降低模具表面硬度,出現(xiàn)粘模、產(chǎn)生龜裂。調(diào)整壓鑄機(jī)的鎖模力,使模具受力均勻。正確選擇(或調(diào)整)充型速度和充型壓力。充型速度(壓射速度)過高會(huì)增大型腔表面由于侵蝕和粘模的損傷幾率,過低充型速度,雖然有利于氣體排出,但會(huì)使鑄件機(jī)械性能下降和表面質(zhì)量變壞。同理,充型壓力增大,也會(huì)使噴嘴充型速度增大。總之,要調(diào)整一個(gè)適度的數(shù)值。在中斷壓鑄澆注作業(yè)時(shí),切記要關(guān)掉冷卻水,以免使模具溫度下降太多,以致恢復(fù)澆注作業(yè)時(shí),影響鑄件質(zhì)量和模具壽命。
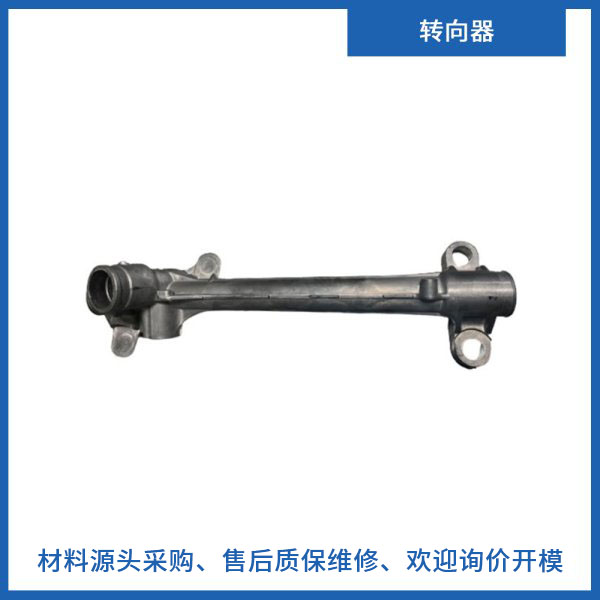
選擇合適的脫模劑及正確的噴涂方式:壓鑄時(shí)要將脫模劑噴涂在于金屬溶液接觸的型腔表面,其主要作用是避免金屬液粘附在型腔表面和保證鑄件與型壁分離,延長(zhǎng)模具壽命。脫模劑有水劑、油劑,近年來還研制出粉劑和顆粒狀脫模劑。要求:脫模劑不能對(duì)鑄件表面質(zhì)量有不良的影響,無氣味冒煙發(fā)生,也不得留下殘留物。脫模劑濃度要適當(dāng),要經(jīng)常攪拌,千萬不能讓其沉淀,否則模具型腔會(huì)因?yàn)闃O冷引起熱疲勞龜裂。噴涂量要少,噴的要均勻,形成的膜要薄。噴涂太多太厚會(huì)造成鑄件疏松、夾渣、起泡、氣孔等缺陷。如水劑脫模劑噴涂效果不佳,應(yīng)選擇油劑脫模劑或粉劑脫模劑。但要在真空狀態(tài)下使用。鑄件脫模快、生產(chǎn)率高、質(zhì)量好,而且模具產(chǎn)生的熱應(yīng)力較少,有利于延長(zhǎng)模具使用壽命。
確保澆注的鋁合金質(zhì)量:保證鋁合金的成分;鋁合金熔化與保溫槽必須分開。中央熔煉要嚴(yán)格控制氣體如氧化物的含量、避免把廢品和回爐料直接加入保溫爐中,否則會(huì)污染金屬液,不但嚴(yán)重降低鑄件的質(zhì)量,更會(huì)容易造成粘模及腐蝕模具。鋁合金溶液 Fe 的含量應(yīng)控制在 0.7~1.3%之間,如果低于 0.7%則容易引起粘模現(xiàn)象,如果大于 1.3%則會(huì)形成金屬化合物硬質(zhì)點(diǎn),產(chǎn)生沖蝕。建立良好的模具維護(hù)制度,使模具處于良好的工作狀態(tài):及時(shí)清洗和打掃模具,去除型腔殘留物和飛邊;更換或修復(fù)已損壞的零件;定期對(duì)模具進(jìn)行消除應(yīng)力處理:首次去應(yīng)力處理為,初期投產(chǎn)模具使用約 2000~5000 模次時(shí);第二次去應(yīng)力處理為,使用 10000~20000 模次時(shí);其余每次去應(yīng)力處理間隔同上,最大不能超過 15000 模次。模具使用一段時(shí)間之后,檢測(cè)模具表面硬度有所降低,出現(xiàn)粘?,F(xiàn)象時(shí),應(yīng)將模具表面研磨光滑,進(jìn)行一次軟氮化處理,滲氮層厚度為 0.08~0.12mm,或軟氮化+氧化復(fù)合處理,它將有效的提高模具的使用壽命。